クレーンの設計計算に於ける係数(安全係数:作業・衝撃)使用頻度に対する考慮を,構造規格の経緯に合わせ考え方を示す。
5.1 S37年10月31日(労働省告示53号)
〜S46年10月21日(労働省告示54号)〜
この告示「構造規格」の構造部分は,当該クレーンの使用に「支障となる変形等が生じないように剛性が保持されているものでなければならない」(14条)と記載され,寿命に対する想定は無く,クレーンの種類によって計算における「割り増し係数」(構造体に対する安全率)を加味する事となっていた。【表1】参照
また,巻上装置に関しての規格である,ドラム,シーブにおける大きさ(D/d:ロープとの直径比)では20倍以上,エコライザー(釣合車)は10倍以上と決められている。
表1 昭和46年割増し係数・静荷重係数φ
旋回速度又は走行速度m/min |
係数φ |
0 |
1 |
レール継ぎ目なし |
90≦ |
1.2 |
90> |
1.1 |
レール継ぎ目あり |
60≦ |
1.2 |
60> |
1.1 |
・動荷重係数Ψ
項 |
機 種 |
係数Ψ |
1 |
一般用
かぎクレーン |
小荷重 |
小型巻上機 |
1.2〜1.4 |
2 |
手動クレーン |
1.2 |
3 |
中小荷重(15t以下) |
天井クレーン |
1.4 |
4 |
橋形クレーン |
5 |
壁クレーン |
6 |
塔型ジブクレーン |
7 |
ジブクレーン |
8 |
大荷重 |
天井クレーン |
1.2〜1.6 |
9 |
橋形クレーン |
1.2〜1.4 |
10 |
ジブクレーン |
1.2〜1.4 |
11 |
クラブ付
クレーン |
ヤード |
天井クレーン |
1.6 |
12 |
橋形クレーン |
13 |
ジブクレーン |
14 |
本船場 |
橋形クレーン |
1.6〜1.9 |
15 |
ジブクレーン |
16 |
製鉄製鋼
用クレーン |
高炉巻上機 |
1.6〜1.9 |
17 |
装入クレーン |
18 |
鋼塊クレーン |
19 |
鋳なべクレーン |
1.4〜1.9 |
20 |
鋳入クレーン |
21 |
原料クレーン |
22 |
鋼片クレーン |
23 |
鍛造クレーン |
24 |
焼入クレーン |
1.6〜1.9 |
25 |
特殊クレーン
その他 |
浮クレーン |
1.2〜1.4 |
26 |
修理用クレーン |
1.2〜1.4 |
27 |
組立クレーン |
28 |
コンクリート
打用 |
ケーブルクレーン |
1.4〜1.6 |
29 |
高速ジブクレーン |
1.6 |
30 |
― |
1.2 |
5.2 S51年8月5日(労働省告示第60号)全面改正
全面改正された規格に於いて「第12条剛性の保持」に構造部分は,壁面座屈(板で構成される構造部分の局部座屈),著しい変形等が生じないよう剛性が保持されているものでなければならないと記され鋼構造部分の耐用年数は20年(ISO,FEMの考え方:1984年クレーン誌第22巻11号に記載)と想定し,この間にクレーンが定格荷重に対しての荷重率で,荷重を受ける回数を想定する。
頻度に応じT群〜W群に分類し,クレーン鋼構造部分がその寿命の間に受ける荷重の大きさ,その変化及び衝撃を考慮して「衝撃係数」「作業係数」を乗じて割り増し,あたかもこの大きさの荷重が加わったものとして取り扱うとされた。
「衝撃係数」とは,巻上荷重を割増す係数で,荷重を地切りする場合等に大きな衝撃荷重が加わる事とし,この衝撃の割増しをするものとされた。
「作業係数」とは,巻上荷重,自重,水平荷重を割増す係数で,クレーンの作業条件及び重要性を考慮して割増を行う。【表2】
また,巻上装置に対する計算基準(ロープとの直径比:D/d,安全率)も,この分類において加味されている。
これらの事から改正前に比べ,より設計基準が具体化され,寿命の考え方が反映されてきた。
ここでのクレーン群に於いてクラブ式は任意のT〜W群の頻度に応じて設計されており,ホイスト標準品に関してはU群にて設計されている。
5.3 H7年12月26日(労働省告示第 134)全面改正
〜新構造規格についての主な変更点〜
主要海外規格(ISO,FEM)との整合性確保のため,(昭和51年8月5日告示第80号を廃止)労働安全衛生法第37条第2項及び第42条の規定に基づきクレーン構造規格が平成7年12月26日(労働省告示第134号)に新たに制定,平成8年2月1日適用となった。以下,構造計算に於ける旧規格との主な相違点(クレーン構造規格関係)を示す。
(1) |
構造部分に,使用できる鋼材を追加するとともに,外国規格等に適合する鋼材であって同等以上の化学成分及び機械的性質を有する鋼材は使用できることとし,それに伴う所要の整備を行った。
(第1条,第3条,第4条関係) |
(2) |
国際単位系との整合性を図るため,力の単位を「ニュートン」とし,それに伴う所要の整備を行った。
(第2条,第3条,第5条,第9条,第17条,第41条関係) |
(3) |
建築基準法令との整合性を図るため,木材の許容応力の見直しを行った。(第5条関係) |
(4) |
労働省労働基準局長が認めた場合には,風荷重及び地震荷重を他の方法により求めることができることとした。
(第9条及び第10条関係) |
(5) |
ISO規格等との整合化を図るために,衝撃係数(巻上速度にて計算)作業係数【表5】,吊り上げ装置等(巻上等級)【表3】のドラム等のピッチ円の直径と当該ドラムに巻き込まれるワイヤロープの直径との比の値(以下「D/d」という。)及びワイヤロープの安全率を見直した。
(第11条,第20条,第54条関係) |
(6) |
構造部材又は溶接部分の破損の発生に鑑み,疲労の考慮を新たに規定したものである。(第12条関係) |
(7) |
天井クレーンのたわみの限度について適用を除外する規定を設けた。(第14条関係) |
(8) |
走行ブレーキを必要とする走行クレーンを見直すとともに,横行ブレーキを必要とするクレーンについて新たに規定した。(第18条及び第19条関係) |
(9) |
人力で走行するクレーンに対する規制を緩和した。
(第30条及び第40条関係) |
(10) |
外れ止め装置に適用を除外する規定を設けた。
(第32条関係) |
(11) |
床上で運転しクレーンの移動とともに運転者が移動する方式のクレーンについて,走行及び横行速度の制限を設けた。
(第33条関係) |
(12) |
停電によりクレーンが停止した際に,復旧通電時に不意にクレーンが動き出す事による危険を防止する為の規定を追加。(第34条関係) |
(13) |
コントローラに係る規定を整備した。(第35条及び第36条関係) |
(14) |
トロリー線の感電防止し措置をクレーン本体側でも行えることとした。(第37条関係) |
(15) |
緩衝装置をトロリー等移動する部分に設けることができることとした。(第39条関係) |
(16) |
運転室等のつりチェーンについて追加して規定した。(第49条) |
(17) |
吊りチェーンをリンクチェーンとローラチェーンに分け,その使用基準を定めた。(第55条関係) |
(18) |
以下クレーン等安全規則に稼動状況に於ける条文があり,使用に際しては,「当初の設計された使用条件を留意しなければならない」と記されている。 |
第17条の2(安全規則) |
(設計の基準とされる負荷条件) |
事業者はクレーンを使用する時,当該クレーンの構造部分を構成する鋼材等の変形,折損等を防止する為,当該クレーンの設計の基準とされた荷重を受ける回数及び状態として吊る荷の重さ(以下「負荷条件」という。)に留意するものとする。 |
〜上記第17条の2の解説〜
構造部分を構成する鋼材等が交番荷重を受ける場合には,鋼材等が疲労破壊を起こすおそれがあるので,クレーンの製造に当っては,負荷条件を基準として設計されている。
本条は,使用時における鋼材等の疲労破壊を防止するため,設計の基準とされた負荷条件を超える負荷条件で,クレーンを使用しないよう留意することについて規定されたものである。尚,クレーンの使用条件を考慮した適正な設計を確保する事から,クレーンを設置する事業所は,クレーンの製造又は構造部分の変更を発注をする時は,製造者に対し,負荷条件を明示且つ,設計の基準とされた条件も確認するよう努める。
〔鋼材等〕の〔等〕は,クレーンの構造部分を構成する鋼材の接合部(溶接部,リベット部)が含まれる。
〔荷重を受ける回数〕とは,予想されるクレーンの耐用期間中の回数をいうものであり,具体的には【表5】の荷重を受ける回数をいうものである。
〔常態としてつる荷の重さ〕とは,常態として〕及びドラム,シーブの屈曲径の大きさ(D/d)即ち疲労破断によるリスクを下げるためで,ホイスト標準品に付いて言えば,巻上等級はD級に対応している。
疲労破断は,ロープの安全率と D/dの関係から,構造規格に於いては,つり上げ装置等のドラム及びシーブのピッチ円の直径比の値はロープの種類に応じた(D/d)Sにて,ロープの安全率(第54条第1項第1号の表での値を越えるもの)を加味した計算(但し巻上等級がAに該当する場合は決められた値以上とする)において決定可能である。
巻上等級は巻上装置に対する規定であり,荷重率及び使用時間で規定されている。
例えば巻上頻度は低いが巻上揚程が長い物や,巻上速度が遅とは,定格荷重に対して実際に吊られる荷の重さをいうものであり,具体的には【表5】の区分をいうものである。
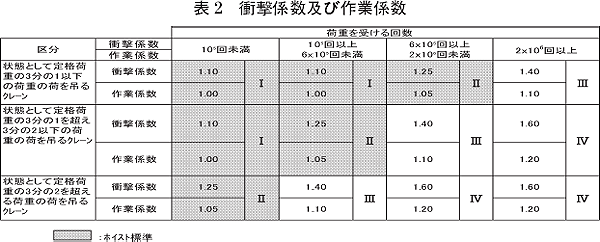
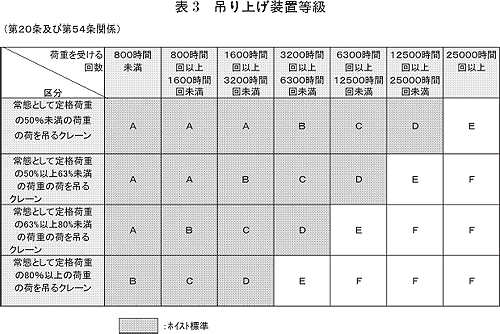
5.3.1構造規格に於ける巻上等級(第20条ドラム等の直径比)
ワイヤロープにより荷の吊り上げ,走行,トロリーの横行等,作動装置(以下「つり上げ装置」と言う)のドラムのピッチ,円の直径と,当該ドラムに巻込まれるワイヤロープ直径との比の値,吊り上げ装置等のシーブのピッチ円の直径と,当該シーブを通るワイヤロープ直径との比の値,又は吊り上げ装置等のエコライザーシーブのピッチ円の直径と,当該エコライザーを通るワイヤロープの直径との比の値は,次の表に……と記されている。【表4】は一般的に使用されるロープ【1グループのワイヤロープ】の構造規格での(D/d)Sである。
巻上等級について要訳すると規定されているのは,巻上装置の使用頻度(荷重率,使用時間)で分類された等級でのワイヤロープの破断に対する安全率,い物はロープの屈曲使用時間が長くなり,等級が上がる傾向に有る。
構造体に対する疲労に関してのリスク規定は,作業,衝撃係数による割増係数であり,荷重率と使用回数(地切り回数:荷を上げる回数)で決定する。
クレーンの使用頻度(グレード)は,巻上等級及び作業における頻度(作業係数)で,使用状況の特定をするべきである。
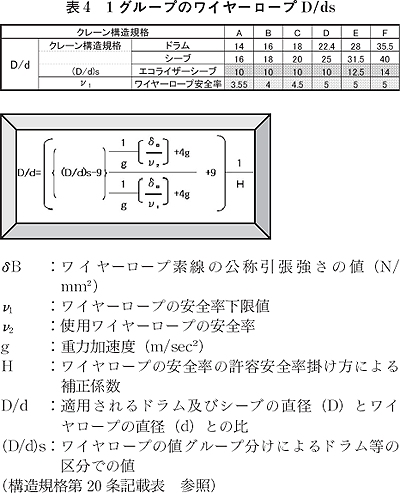
5.3.2使用頻度に於ける構造部分に対する考慮
クレーンに於ける構造部分での強度計算では,
【T】使用頻度による「作業係数」
【U】巻速による「衝撃係数」
【V】荷重の組合せ等による「割増係数(安全率)」
これら【T】【U】【V】を,考慮して計算する。
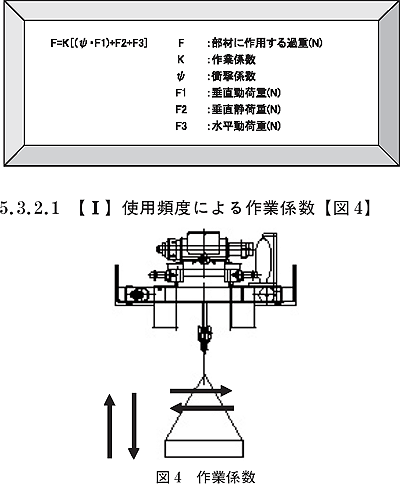
クレーンが荷重を受ける割合と荷重を受ける回数に応じて荷重を割増しする為の係数【表5】
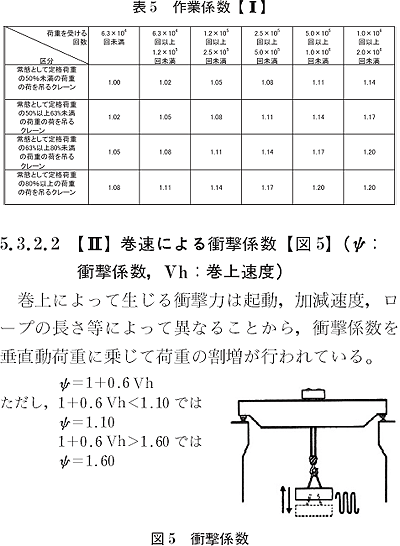
5.3.2.3【V】荷重の組合せ等による「割増係数」
構造規格に於いて破損による落下等,重大災害に.がる主要構造部分に関して,強度的疲労などは,考慮規定されており,各々クレーンの使用状況に応じ,組合せの荷重に対して補正係数(割増係数)を加味し,使用材料に於ける強度での許容応力が決められている。
V |
-1衝撃係数を乗じた垂直動荷重,作業係数を乗じた垂直静荷重,同じく作業係数を乗じた水平動荷重,並びに熱荷重の組合せ |
V |
-2衝撃係数及び作業係数を乗じた垂直動荷重,作業係数を乗じた垂直静荷重,同じく作業係数を乗じた水平動荷重,熱荷重並びに,クレーンの作動時における風荷重の組合せ |
V |
-3垂直動荷重,垂直静荷重,熱荷重及び地震荷重の組合せ |
V |
-4垂直動荷重,垂直静荷重,熱荷重及び衝突荷重の組合せ |
V |
-5垂直静荷重,熱荷重及びクレーンの停止時における風荷重の組合せ |
以上の荷重の組合せにおいて,構造部分の強度に関し最も不利となる組合せによって計算するものとされている。
5.4疲労設計で考慮すべき荷重
5.4.1垂直動荷重【図6】
定格荷重にフックブロックやクラブバケット,吊ビームなどの吊具の質量を加えた荷重がクレーンに作用することによって生じる力。
5.4.2垂直静荷重【図7】
クレーンを構成する部分のうち,垂直動荷重に含まれない部分の質量によって生じる力。
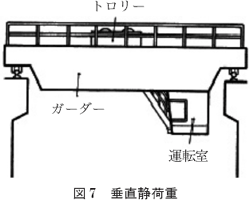
5.4.3水平動荷重【図8】
クレーンの走行,横行,若しくは旋回に伴う慣性力,又は遠心力によって生じる力。
又,走行レールのスパンの精度やクレーンの斜行等により,進行方向と直角に車輪が働く「車輪側方力」などが含まれる。

5.5構造規格で決められている許容応力
割増係数を含んだ荷重の組合せにより計算した応力は構造規格において,使用材料による許容応力以下にする。
決められている許容応力は使用材料の応力変形後,復元する弾性限度内とされているが,繰り返し応力を受け続けるとその強度が次第に小さくなり,やがて変形,あるいは破損にいたる。
構造規格,第12条に(疲れ強さに対する安全性)構造部分は,疲れ強さに対する安全性を確認する事と記され,計算による確認としてJISB8821(クレーン鋼構造部分の計算基準の6.4疲れ許容応力等の基準に基づく確認があるとされている。
経年による疲労に対するリスク評価とし当初の設計根拠とした使用頻度の重要性が求められている。 |